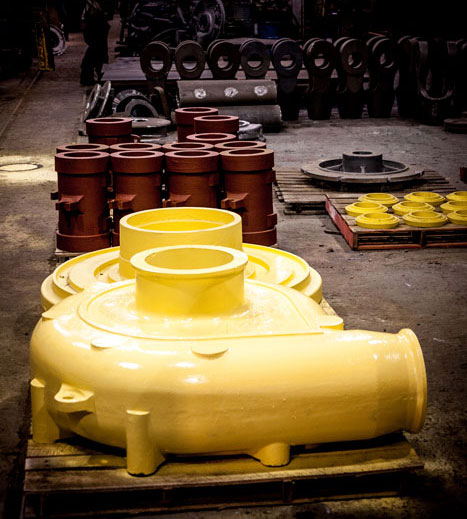
From blueprint to delivery, Weatherly Casting use a fully integrated process that is designed to meet your needs and just-in-time inventory schedule or Kanban(TM) requirements.
Once your project’s specifications are reviewed and verified, our skilled craftsmen will begin by fabricating custom patterns using durable timber or resin. Our experienced workforce handles complex stainless steel and alloy designs with intricate core and mold work.
Those patterns are used to create molds of resin silica or zircon sand. This produces an air-cured silica mold of high rigidity and quality. Most molds are “flow coated” with a zircon refractory coating to give an excellent surface finish.
Once a mold is cured, our craftsmen pour the alloy into the mold and allow it to cool. In order to ensure the finished product will meet or exceed your specifications, each heat is sampled and tested.
Next, the molds are shaken apart, leaving behind the cast piece. We then “rough” clean your product, first using steel shot or grit, then using swing-frame cutters and grinders for the fine work. Your product can be hand cleaned using air grinders. Air-arc cutters are used on stainless steel and high alloys.
Both Weatherly Casting have heat treatment furnaces to further condition your castings. The furnaces reach temperatures up to 2,200 degrees Fahrenheit (1,200 degrees Celsius), and they offer multiple monitoring locations to ensure precise, even tempering. Water quenching is available for steel and stainless steel.
Our specialized and highly-skilled assembly shop facilitates total process control and timely deliveries. Our assembly shop workers are meticulous, paying close attention to detail and quality.
From start to finish, Weatherly Casting know quality production.
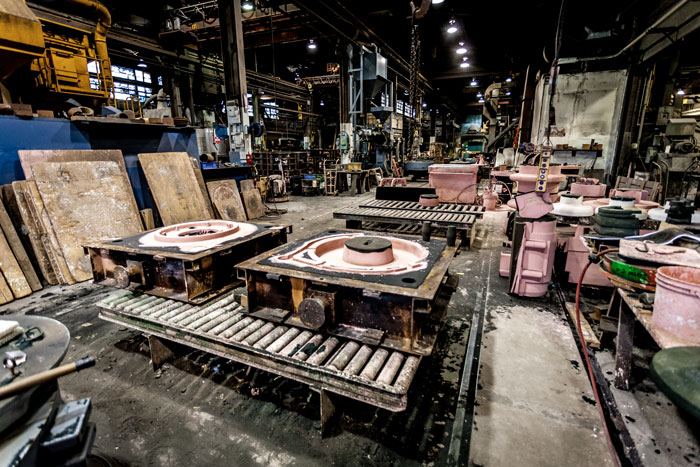